How to Overcome Shipping and Logistics Challenges
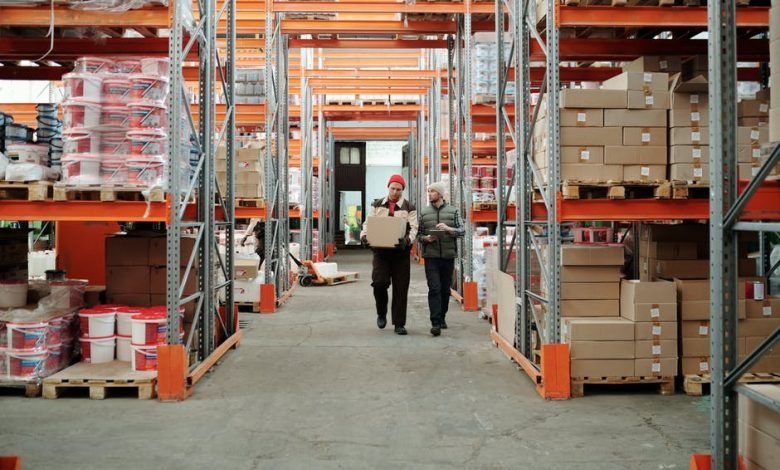
When you’re in the business of warehousing and shipping, you know how hard it can be to stay on top of logistical challenges.
Businesses both large and small depend on you to fulfill orders and keep the shelves stocked, and you risk losing business if simple errors start adding up. How can you make improvements to avoid common shipping and logistics issues?
Today, we’re going to look at everything from transportation costs to freight management to discuss the hurdles you’ll need to overcome.
Read on to learn more about improving your warehousing and shipping business by tackling shipping and logistics challenges.
Improve Delivery Service
During the height of the pandemic, we saw a huge shift in e-commerce that hasn’t fizzled out. Everyone is looking to make online purchases, which means that more businesses are jumping on the product shipping bandwagon. As a result, the warehousing and trucking industry is busier than ever before in storing and transporting goods.
The problem is that supply chain and labor shortages are creating serious shipping delays. Focus on expanding your fleet and securing backup suppliers that can fill supply chain gaps. Automate order fulfillment processes to free up workers who can focus on other stages of fulfillment and shipping.
Reduce Transportation Costs
Gas prices and the cost of freight management are on the rise and we don’t expect them to drop any time soon. Without a proactive solution, you’re going to face a major rise in transportation costs. Now may be the time to start investing in an all-electric or hybrid fleet to reduce reliance on fossil fuels and reduce the need for costly maintenance.
Whether or not you intend to go electric, it’s also a good time to start opening micro-fulfillment centers between your major warehouses. Reducing transportation distances is a must to accommodate an electric fleet and can help to reduce transportation costs across the industry.
Strengthen Communication
When communication isn’t streamlined, you’re bound to face missteps. This includes communication with:
- clients and business partners
- fleet drivers
- warehouse workers
- third-party warehouses you utilize to fulfill long-distance orders
Gone are the days when you can rely on stray emails and phone calls to stay on top of logistics. You need real-time communication solutions and you should consider partnering with an IT team to manage them. A cloud-based system is ideal, as it allows for remote access to key information no matter where your team is located at any given time.
Establish Consistent Practices
One of the biggest logistics challenges comes from inconsistent practices from one warehouse or client location to another. For example, if your driver is used to one docking method but not all of your warehouses use that method, it’s going to create delays and even failed deliveries. The same goes for client locations, which may not have the latest docking technology.
As an industry leader, it’s up to you to establish standard practices for all of your warehouses and delivery locations. This may involve withholding contracts until clients make changes. While this can seem counterintuitive to expanding your business, it will lead to improvements in the long run.
Reduce Warehouse Errors
Common warehouse errors are one of the primary sources of financial loss in the industry. These errors include things like:
- picking errors
- inventory loss
- inventory damage
- health and safety mismanagement
- inaccurate inventory tracking
While it may seem like these issues have a low financial impact, they add up quickly. For example, picking errors alone can create an 11-13% loss in profits.
Warehouse issues tend to come down to two problems: lack of automation and lack of training. The right automation system can reduce inventory loss and inaccurate tracking almost entirely. Proper training can reduce human error and lead to a safer workplace with fewer accidents and injuries.
By addressing warehouse errors, you can increase profits substantially. This can make way for added improvements, such as investing in an electric fleet or improved warehouse technology.
Invest in Better Technology
Because technology is changing at a fast pace, it’s easy to get caught up in the flashiest new thing. Many industry leaders find themselves investing in tech that they don’t need or that doesn’t fit their budget long-term. Cloud-based technology eliminates the need for a lot of software and gadgets.
If there’s any flashy new tech you may want to consider, it’s AI. AI can improve communication both in-house and with clients. Once again, you may want to partner with an IT firm to get the best technology for your purposes and stay on top of any needed maintenance.
Improve Marketing
All of the positive changes you make to your business won’t matter if you aren’t securing new clients. It’s also important to invest in marketing so that businesses seek your shipping solutions for their order fulfillment.
Your website is the first place businesses will look to learn about your location, freight rates, and more. If it’s outdated (or you don’t have a website at all), you’re going to lose a lot of traction off the bat. EZ Freight Broker Trucking Websites makes it easy to design a sophisticated and functional website for your business.
Don’t Get Stumped By Shipping and Logistics Issues
Shipping and logistics errors will always arise in the industry. Your ability to meet and overcome those challenges will allow you to thrive in this world of online shopping.